Front Electric Sustainer | LZ Design
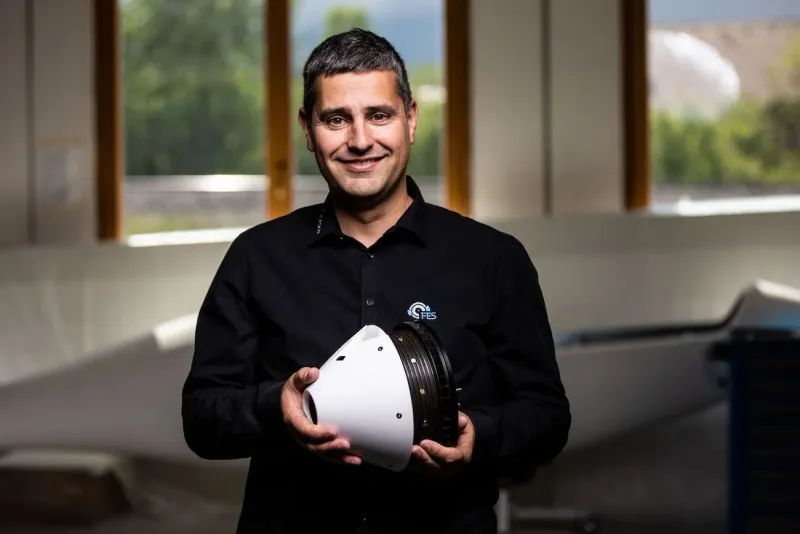
Luka Žnidaršič is certainly one of the persons who have had the most impact on gliding in recent years. He has developed the Front Electrical Sustainer (FES) system and has been working on electric propulsion for sailplanes out of Slovenia for more than 15 years.
Luka, tell us about your company's vision, and how it all started.
I was a pure glider pilot who enjoyed competition flying. At that time, available engine systems were not something I would like to have on my competition glider for many different reasons.
With the development of powerful lithium-ion batteries and brushless motors, I saw an opportunity to develop a reliable front-mounted motor system, where power could be available instantly, with many other advantages. In October 2009 I made the first test flight with a system mounted on my LAK17A sailplane which was a perfect testbed.
How many people work at LZ Design now?
Currently 7 people with full-time jobs.
How many FES systems do you produce?
In recent years we have produced about 40 FES systems per year. Altogether more than 350 FES systems flying, on 24 different types of sailplanes.
How have the batteries improved since the first installed FES system?
From our first FES GEN1 battery packs, we made a lot of improvements, mainly about safety and energy storage capacity.
In spring this year our latest FES GEN4 battery packs finally passed safety tests according to EASA's latest requirements. The first samples of GEN4 packs have been provided to all major FES glider manufacturers. Each manufacturer prepared flight test reports and applied for so-called technical notes to approve them for usage on their different types of FES gliders.

What are the advantages of GEN4 over GEN3?
The older GEN3 still has Kokam pouch cells like GEN2, but with higher cell capacity (53Ah instead of 40Ah of GEN2), with a new e-paper display and g-sensor electronics.
New GEN4 has cylindrical 18650 cells (18mm diameter, 65mm long), and they are available in four different versions: Two versions (14S 56Ah, 16S 56Ah) for single seaters and two versions (14S 84Ah, 16S 84Ah) for double seaters.
What is the difference between these four versions?
The difference is in the number of cells wired parallel (20 for single-seaters and 30 for double-seaters), and the number of such cell blocks in serial (14 or 16). These numbers determine the battery capacity and voltage level.
The single-seater versions have a capacity of 5.6 kWh (14S) and 6.4 kWh (16S) and the double-seater versions have 8.4 kWh (14S) and 9.6 kWh (16S).
What increases do you expect in the future?
It is very difficult to predict the future. It is not clear how soon the efforts of scientists will provide better batteries. I suspect that without a complete change of battery cell chemistry, there are not many possibilities left, to increase both capacity ratio (Wh/kg) and power ratio (W/kg) simultaneously, without compromising safety.
So you do not expect GEN5 to make any leaps in capacity?
I hope so, but at this moment I do not see any possibility for GEN5.
Have there been any problems with the reliability of older systems?
I am surprised by how reliable even the oldest FES systems are.
You sometimes go flying with a DuoDiscus FES. Do you think battery technology has now reached a sufficient level for a good range in double-seaters?
For a Duo Discus FES, about 7 kW of power is required to keep it in level flight at 100km/h, whereas you only need around 4 to 5 kW for an 18m single-seater.
With GEN4 we have finally managed to achieve that double-seaters have the same range single-seaters have had with GEN2. About 100km of level flight is now realistic with a double-seater. This means 1h of powered flight.
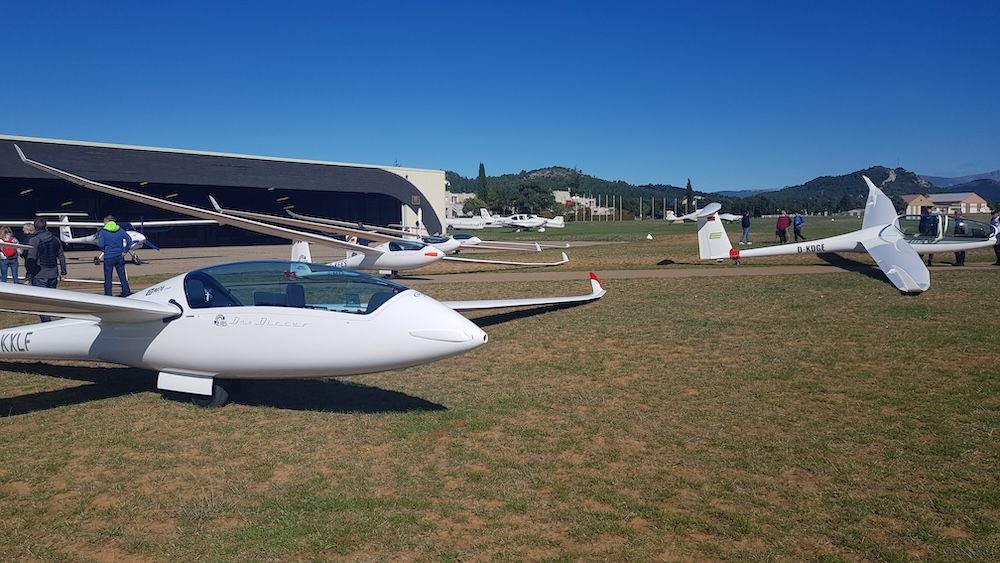
When will we see the Arcus FES?
The latest price list of Schempp-Hirth already includes Arcus FES. The fuselage is nearly identical to Duo Discus FES, so I hope we will see the first Arcus FES in the not-too-distant future.
Which batteries will it have?
Into the Arcus it would be possible to install the heavier 16S version of GEN4 (like with the DG1001) as there is no problem regarding the maximum weight of non-lifting parts. The range will be more than 100 km.
For the DuoDiscus, a lighter 14S version is planned.
Do you expect to see more gliders being able to FES-self-launch in the future?
So far already one-third of all FES gliders are self-launchers (Silent 2 Electro, MiniLAK FES, AS13.5m FES, AS15m FES, Versus, LAK17C FES).
A few years ago, we already managed to get more than 30kW out of the system with some changes. With that power, even heavier 18m FES gliders are capable of self-launching without water ballast (LAK17C FES, Antares FES). The main requirement is of course a sufficiently high landing gear to achieve the required propeller clearance. This can be done on a Ventus 3 FES without too much work.
What kinds of improvements in the engine will we see in the future?
We are always trying to improve our products. Recently we found a good solution for better cooling of the motor and also for further improving the motor efficiency at high power settings. This means future FES motors will have an even lower temperature rise at high power.
The bigger the prop, the higher the efficiency. How does the FES compare to aircraft fitted with an electric retractable engine in terms of efficiency?
The efficiency of powered flight is not just about propeller size. A bigger propeller needs to rotate slower and so requires an electric motor with a bigger diameter to provide sufficient torque.
Such a big motor on top of a pylon exposed in the airflow produces a lot of drag. It is like flying with half-open air brakes, and as a result, much more power from the engine is required.
You are saying that big propellers on the RES do not make sense?
No, I am just saying that the exposed engine and pylon in the airflow lead to a lot of drag, about the same amount as a complete glider, so even a big propeller with good efficiency can not offset the poor efficiency due to the exposed pylon and engine.
On the other hand with FES there is still a very aerodynamically clean powered flight, so cruising with FES can even be done at 150km/h, with a very small increase of power.
E-glide competitions have proved that the efficiency of the FES system is superior compared to any retractable system. Only 4-5kW of power is required for level flight with an 18m FES glider. For comparison, our RES system installed on ASG 29 needs 7-8kW for level flight.
Are there different propeller diameters of the FES system?
Yes, we have 1 m, 1.02 m, and 1.2 m diameters of propeller. The FES system on Antares has a 1.2 m prop diameter which is the same prop diameter as on JS3 RES.
For the Discus and Arcus, we use the 1.02 m propeller, as there is no space for the longer engine version which is required for the 1,2m propeller.
The FES blades still cost a bit of drag when they lay on the fuselage. Any chance to have them fit more neatly in the future?
During many competition flights on the highest level, it was not possible to recognize any performance difference due to FES blades when compared to other non-FES gliders. Most of the glider drag is due to its wings, and the fuselage provides only a smaller portion, which mostly depends on its cross-section.
With existing fuselages, it is hardly possible to make them more neat. But if we would design a dedicated FES fuselage, some further improvements would be possible.
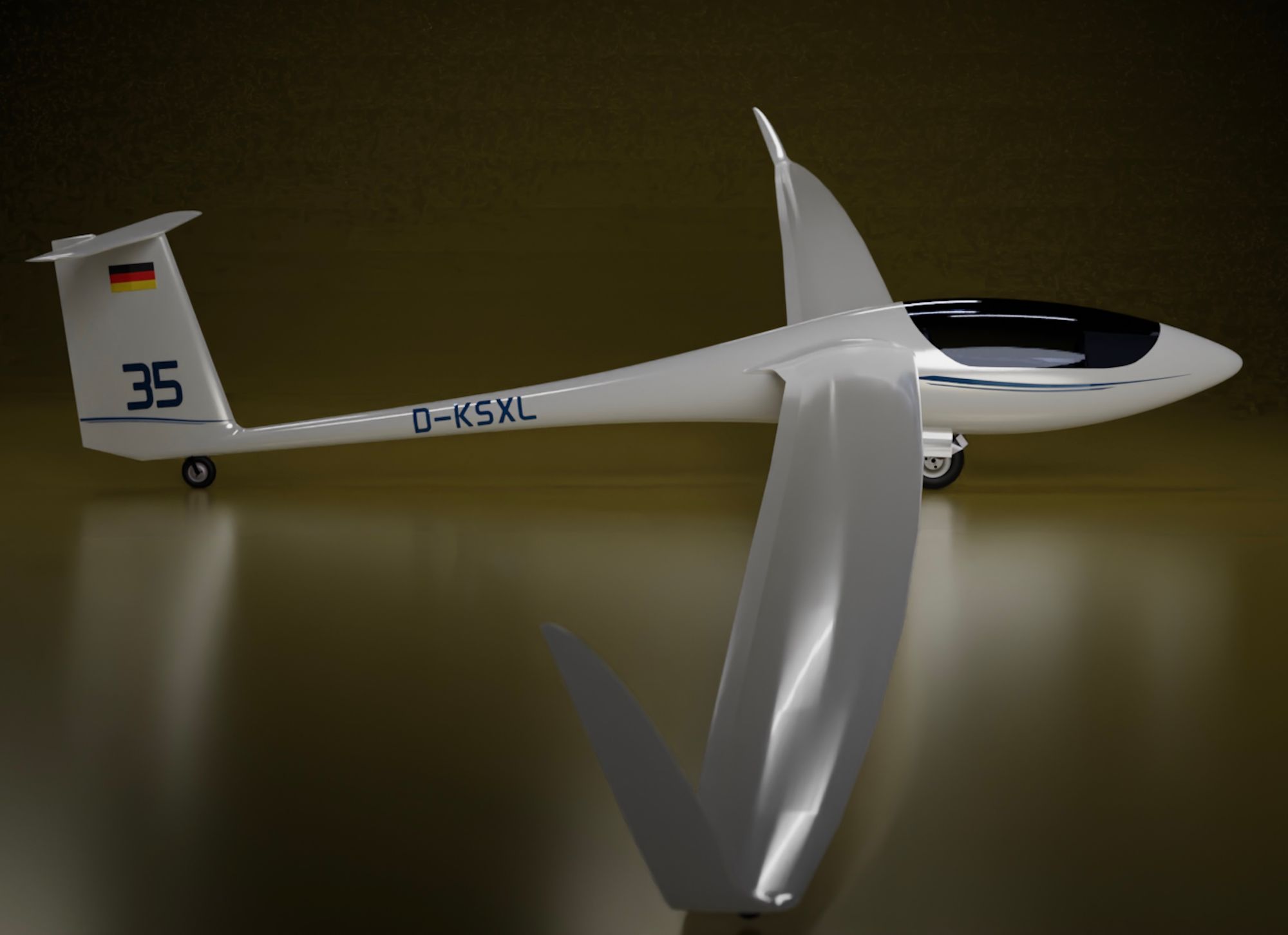
At the moment, you are the only manufacturer of the FES system. Do you think that will change at some point?
There are already some copies of our FES system, but all are quite rough around the edges.
So there are no patents that prevent other companies from copying the system?
Patents are very expensive, their protection is questionable and they have a time limit. EASA paperwork is more important. We have an EU-registered FES and RES as our trademarks.
A lot of new gliders are being offered with retractable electric engines.
Most of the available self-launching gliders are not top competition models. They provide freedom but request a lot of maintenance.
Electric retractable systems promise less maintenance, but at the cost of a pretty high minimum wing loading (50 kg/m2), when installed on the latest top competition gliders with small wing surfaces. The minimal wing-loading of most FES-equipped gliders is much lower, about 42 kg/m2.
Indeed new airfoils can carry high-wing loading pretty well, but in poor weather conditions, a low wing-loading is still a big advantage.
Another big advantage of FES is that in stressful situations the full power is available immediately, without any altitude loss. There is no stressful phase of pylon extraction, and no need to plan engine starts only in certain areas, from which it would be possible to glide with an extended pylon to a safe outlanding area in case the pylon would not be possible to retract.
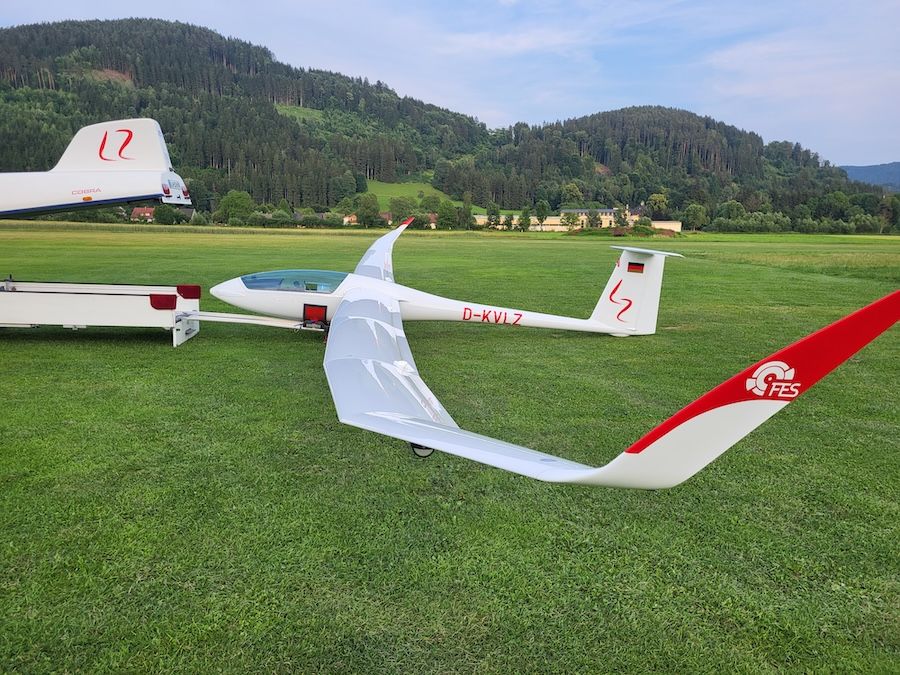
Are you planning to develop other electric propulsions in the future?
We have already developed our own RES system on customer request. It is installed on a turbo-prepared ASG29 without any structural modifications. The first flight was in the spring of 2020, before the AS34Me or the JS3 RES.
The request was to be as light as possible, for top-level competition flying, where it is used as a sustainer. It has a minimum wing loading of 45 kg/m2. As such it fits into the rules of e-glide competition max wing loading limit. It is capable of self-launching without water ballast. The maximum climb rate is about 2.7m/s at a max power of 35kW. The maximum system voltage is 125V and the batteries are fixed in the fuselage with a capacity of 6.5kWh.
It is Annex I type (out of EASA, with a national Permit to fly), for experimental and scientific purposes.
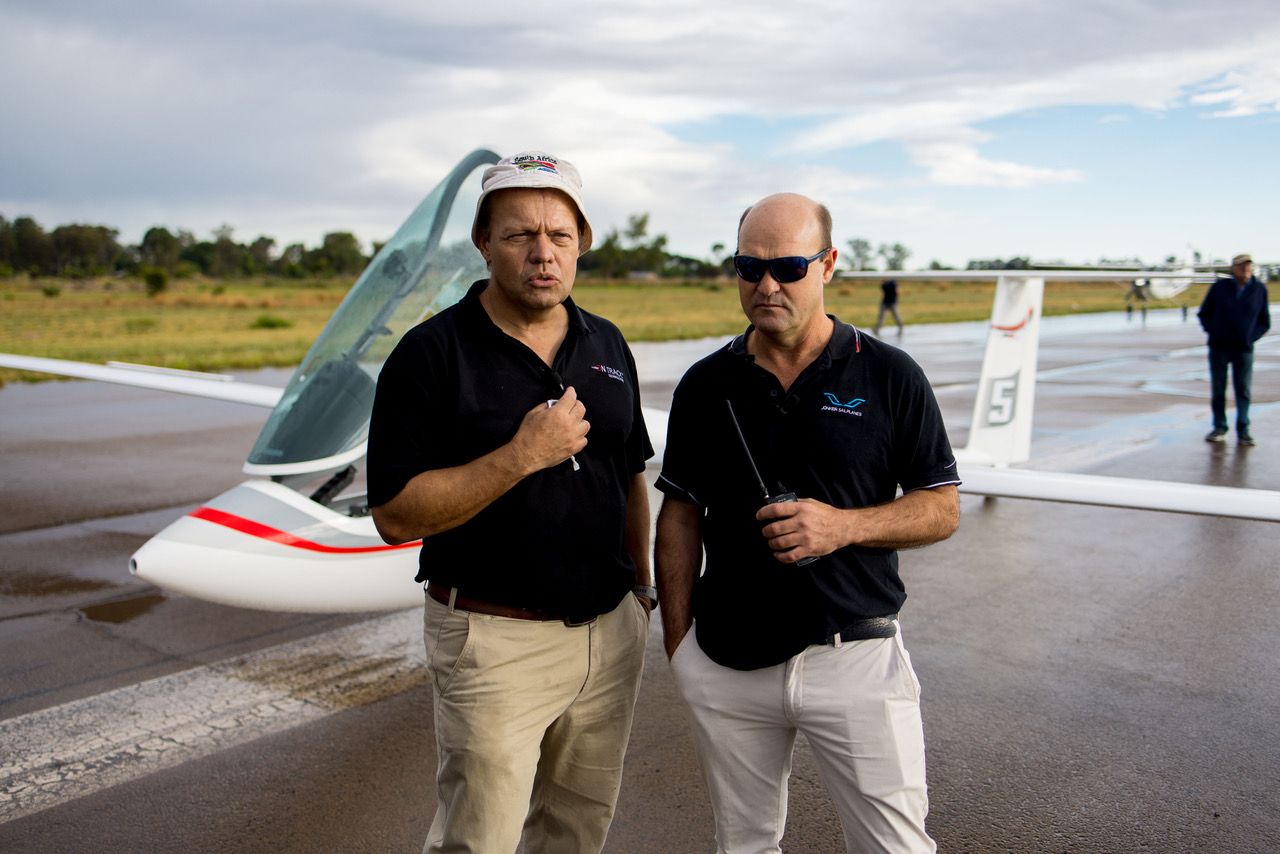
Any plans to cooperate with some manufacturers on this system?
So far we have provided our motors for the Electric Libelle project of Streifeneder. There were a few other projects with our components too.
There are many older gliders without any propulsion system which would greatly benefit from the FES system.
On the recent German Segelfliegertag, Schempp-Hirth announced that FES retrofits to Discus 2c (T) are now possible. Some Ventus 2cxa (j) have also been retrofitted with FES.
We have also retrofitted some US gliders with experimental registrations (ASW27, JS1, Ventus 2cx, ...). Unfortunately, for older European gliders, the required bureaucracy is way too complicated, when modification is done without TC holder (manufacturer) support. There are some possibilities for a national permit to fly.
Up to now, it was more profitable to offer FES mostly for new gliders. Due to the huge price increase of new gliders, retrofitting of existing gliders is now becoming more and more attractive.
It is also possible to retrofit some LS 8b models with carbon fiber wings with the FES system, the exact serial numbers can be found on the website of DG Aviation. Older LS8a are not suitable because of the maximum weight of the non-lifting parts.
Luka, thanks for taking the time to talk with us.
If you enjoyed the article, please consider supporting us:
If you would like to receive the second article of our series about glider manufacturers directly by email, you can sign up for this in your profile: